DSP (digital signal processor) is a unique microprocessor that uses digital signals to process large amounts of information. Its working principle is to receive an analog signal and convert it to a digital signal of 0 or 1. Then modify, delete, and strengthen the digital signal, and interpret the digital data back to analog data or the actual environment format in other system chips. Not only is it programmable, but its real-time running speed can reach tens of millions of complex instruction programs per second, far exceeding the general-purpose microprocessor, it is an increasingly important computer chip in the digital electronics world. Its powerful data processing capabilities and high operating speed are the two most commendable features.
Ice and snow cover threaten the safe operation of power and communication networks [1-4]. Ice coating robot is an automatic device aimed at removing ice coating on transmission lines. The robot needs to perform servo control on various motors such as walking motor, joint motor and gripping and tightening motor. The types and number of motors are relatively large, so the robot control system is relatively complex. This paper mainly studies the servo control of walking motor of ice-covered robot. The walking motor needs to drive the robot to walk on the line. When the line has a large ice coating, it needs to drive the de-icing knife to complete the ice breaking work. During the operation, when the robot encounters the thickness of the ice layer and cannot continue to advance, it will automatically complete the retreat, accelerate the forward rush, and perform intermittent deicing.
The servo control of the walking motor adopts a fully digital brushless DC motor control system with the chip TMS320LF2407 as the core of the motor control special chip. The full digital control method can effectively avoid the interference of unstable factors in analog control. Since the robot works in a strong electromagnetic environment, the fully digital control method can effectively avoid electromagnetic interference. Because the DC brushless motor has a series of advantages such as simple structure, reliable operation and other AC motors, and has the advantages of high speed, high efficiency, high dynamic response and other DC motors, the system selects the DC brushless motor as the robot axis drive ].
1 Overall structure design of control system
By analyzing the motion equation of the DC motor, it can be known that the motor acceleration is proportional to its torque, and the torque is proportional to its current. Therefore, to achieve high precision and high dynamic performance control of the motor, it is necessary to simultaneously control the speed, current and position of the motor Perform testing and control. The system includes a position detection link and a current detection link, which respectively detect the speed and current of the motor. The hardware circuit of the system mainly includes DSP system, power drive circuit, isolation circuit, position detection circuit and current detection circuit. The structural principle of the system is shown in Figure 1.
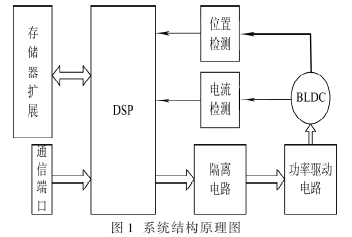
Digital Signal Processing (DSP) is an emerging discipline that involves many disciplines and is widely used in many fields. Since the 1960s, with the rapid development of computer and information technology, digital signal processing technology came into being and has developed rapidly. Digital signal processing is a method of processing real-world signals by performing transformations or extracting information using mathematical techniques, which are represented by digital sequences. In the past two decades, digital signal processing has been widely used in communications and other fields. Semiconductor manufacturers such as Texas Instruments and Freescale have strong capabilities in this field.
2 Speed ​​closed-loop control
A deviation is formed according to the input setting value and the feedback amount, and a series of digital adjustments are made to form the control amount of the PWM duty cycle, thereby controlling the rotation speed or speed change of the servo motor.
Speed ​​closed-loop control is mainly responsible for the control of robot walking speed and speed change during de-icing. Figure 2 shows the double-loop control system of brushless DC motor speed and current. When forming a speed closed-loop control of BLDCM, the rotation direction and rotation angle of the motor are detected by a photoelectric encoder and fed back to the DSP system.
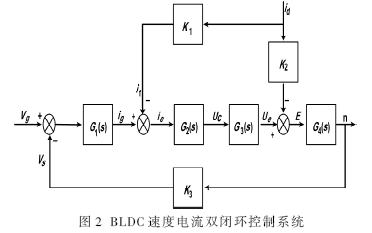
among them,

Is the transfer function of speed PI control, KS is the speed loop proportional coefficient,

Is the time constant of the speed loop;

Is the transfer function of current PI control, KC is the current loop proportional coefficient,

Is the transfer function of the PWM controller, KP is the magnification,

Is the time constant of the first-order inertial link;
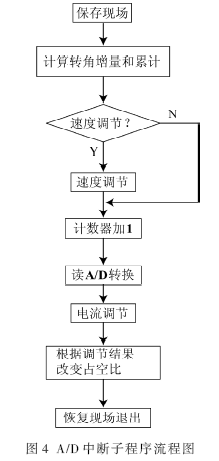
Is the back electromotive force constant of the motor under rated excitation; K1 and K2 are the proportional coefficients of current and speed feedback; K3 = R is the phase resistance of the motor; Ï…g is the given speed of the motor; Ï…s is the motor feedback speed; ig is the speed adjustment The output of the device, that is, the current given value; if is the feedback current; ie is the current error signal; Uc is the PWM control signal; Ud is the DC voltage of the motor; E is the amplitude of the opposite electromotive force of the motor; id is the motor phase current; n is The true speed of the motor.
3 System hardware design
3.1 Phase current detection
Because the main circuit of power electronics adopts two-two energization mode. At any time, the current only flows into two phases of the three-phase winding, so only one phase current detection sensor can complete the detection of the phase current. Use bypass resistors to detect current in each phase. The resistor is located between the lower end power bridge arm of the three-phase fully-controlled power conversion circuit and the ground, and also plays the role of overcurrent protection. After the voltage drop signal on the resistance is amplified, it is sent to the A / D conversion channel on the TMS320F2407 chip, and the appropriate current signal is obtained after A / D conversion. After the A / D conversion is completed, the A / D conversion module will send an interrupt request signal to the CPU, waiting for the CPU to detect the current signal. Finally, according to the current error, at the beginning of each PWM cycle, the duty cycle of the PWM pulse is adjusted [6].
3.2 Rotor position and speed detection
Select TMS320LF2407A to realize the control and drive circuit of three-phase brushless DC motor speed regulation. Using three Hall sensors distributed at intervals of 120 °, the rotor position signal output by the Hall device is sent to the power conversion circuit, and then directly sent to the capture unit of the TMS320LF2407A for processing. Detecting the state of the three capture ports can get the current combined state of the three position signals, and thus get the rotor position. Each transition captured by the capture ports CAP1 ~ CAP3 triggers a capture interrupt, and each time the rotor makes a revolution, 6 capture interrupts are generated. The motor speed is obtained by measuring the time interval between two adjacent interruptions.
3.3 Drive circuit design
The motor control driver uses IR2130 chip. The IR2130 chip controls the turn-on and turn-off sequence of the six power tubes to realize the positive and negative rotation of the motor. The driver chip itself provides overvoltage protection for power devices. It contains a logic protection circuit. When there is a level-through logic, the chip immediately outputs all low levels and turns off all MOSFETs. In addition, there is a detection resistor in the power circuit protection device. When the current is too large, the detection signal is logically judged and the PDPINT is set to low level. The DSP internal counter stops counting. Current protection [7].
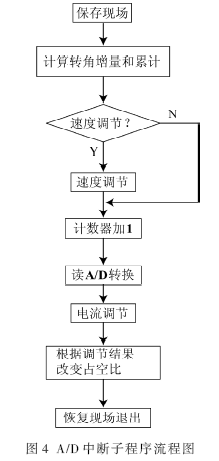
4 System software design
The main program mainly completes the DSP initialization, the flow chart shown in Figure 3. The A / D conversion interrupt subroutine completes the adjustment of speed and current. The flow chart is shown in Figure 4. The experiment clock frequency is 20 MHz, and the PWM frequency is 20 kHz. The A / D conversion is started by the 1-cycle matching event of the timer, so that each PWM cycle has a current sampling, and the current is adjusted in the A / D conversion interrupt handler to control the PWM output. The capture interrupt program finishes counting the position and calculating the speed reference. The program flow chart is shown in Figure 5. Every time the rotor rotates through an angle of 60 °, a capture interrupt is triggered to perform the commutation operation and speed calculation [8].
This paper uses TI's TMS320LF2407A DSP to design a DC brushless motor control system for icing robot walking and de-icing. After analysis, the system is not only low-cost, easy to implement, but also stable in performance and easy to expand, which is of great significance to engineering practice and motor speed regulation. (China Educational Equipment Purchasing Network)
The Clothing cylinder box are used for t-shirts, ties, socks, jeans, underwear, and other apparel. This Clothing Cylinder Box design will save you money, promote an environmentally conscious corporate image to your customers, help your products stand out in the competitive market. The Clothing Cylinder Box can be
with any customize printing and logo to enhance your brand.
Clothing Cylinder Box
Clothing Cylinder Box,Custom Cylinder Box,Clothing Packaging Box,Cylinder Tube Box
Shenzhen Hongte Printing & Packaging Co., Ltd. , https://www.ipackpaperbox.com